An opportunity of industrial transformation — Exploration and practice of industrialized assembled bridge technology
Industrial assembled bridge technology is an innovative technology to prefabricate the main components of the bridge in the factory and then transport them to the site for assembly to complete the bridge construction. It is an effective means to speed up the construction speed, reduce on-site pollution and realize low-carbon construction. At present, the prefabrication and assembly of bridge superstructure has been relatively mature after several years of practice and exploration. Although the assembly technology of bridge substructure started late, it has also accumulated some experience through exploration in recent years. In recent years, with the increasing pressure of transportation, the demand for reducing the impact of municipal construction on daily life is becoming stronger and stronger, and the fabricated bridge technology will have a broader application space.
Assembly connection technology

Figure 1 Shanghai humin viaduct phase II project
Subsequently, in some areas with low seismic risk in the United States and Canada, the application of precast assembled pier technology is gradually increasing. For example, the lower pier of Vail pass bridge in Colorado adopts bonded post tensioned prestressed reinforcement connection. With the further research on the seismic performance of precast assembled columns, the precast assembly technology of columns began to be applied in some seismic risk areas. The American I-5 grand mount to maytown I / C 2-span precast girder bridge built in 2011 is the first bridge project considering seismic performance and using precast assembly technology to build lower piers, as shown in Figure 2. In China, in 2010, Shanghai took the lead in using the grouting sleeve connection technology to realize the construction of fabricated columns in the test section of the new S6 highway project, and comprehensively promoted it in the Jiamin elevated project opened to traffic in September 2016. The project is the first large-scale use of fabricated pier technology in China. Through this technology, the traffic pressure during the construction period is greatly relieved (as shown in Figure 3), and the bridge construction with high quality and short period is realized.
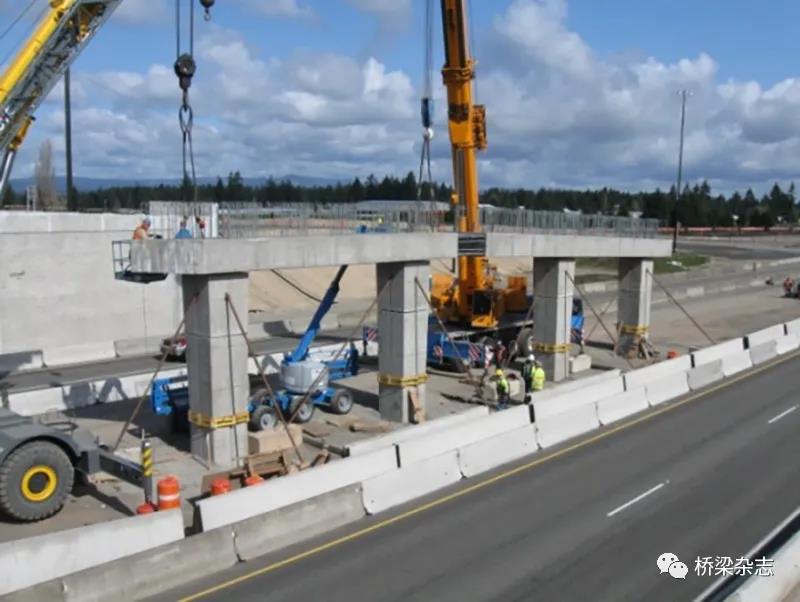
Figure 2 I-5 grand mound to maytown stage 2 Bridge in the United States
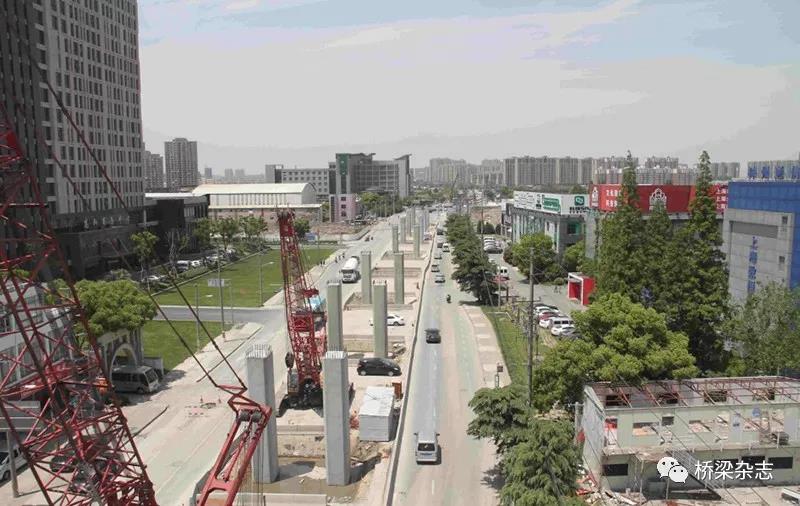
Figure 3 construction of Jiamin elevated fabricated column
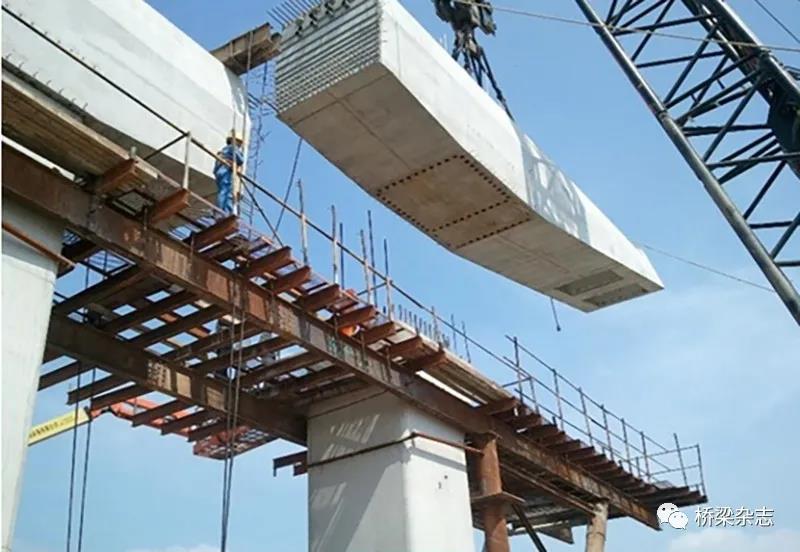
Figure 4 construction of Jiamin elevated fabricated bent cap
Fabricated column
The key of fabricated column is the connection mode between pier, bearing platform and cap beam. At present, the fabricated column connection methods adopted at home and abroad are roughly as follows:
1. Bonded post tensioned prestressed tendon connection
Bonded post tensioned prestressed reinforcement connection structure often cooperates with mortar cushion or epoxy adhesive joint structure to realize the construction of segmental Precast Pier. The prestressed reinforcement in the scheme can adopt high-strength reinforcement such as steel strand or finish rolled deformed steel bar. The structure is characterized by prestressed tendons passing through joints, many practical engineering applications, mature design theory, calculation analysis and construction technology experience; The disadvantage is that the cost of the pier body is much higher than that of the traditional cast-in-situ concrete pier. At the same time, the on-site construction requires tensioning and grouting of the prestressed reinforcement. The construction process is complex and the construction time is long.
2. Grouting sleeve connection
The precast pier body segments are connected with the protruding reinforcement through the grouting connection sleeve. The mortar cushion is often used on the contact surface between the pier body and the bent cap or bearing platform, and the epoxy adhesive joint structure is used between the pier body segments, as shown in Figure 5. The structural characteristics are high construction accuracy requirements, short on-site construction time, no tensioning of prestressed reinforcement, significant reduction of on-site workload, and its mechanical properties under normal service conditions are similar to those of traditional cast-in-situ concrete piers, so it has certain economic advantages. According to foreign application experience, low seismic risk areas have been widely used, and the application and scientific research of high seismic risk areas are still in progress.
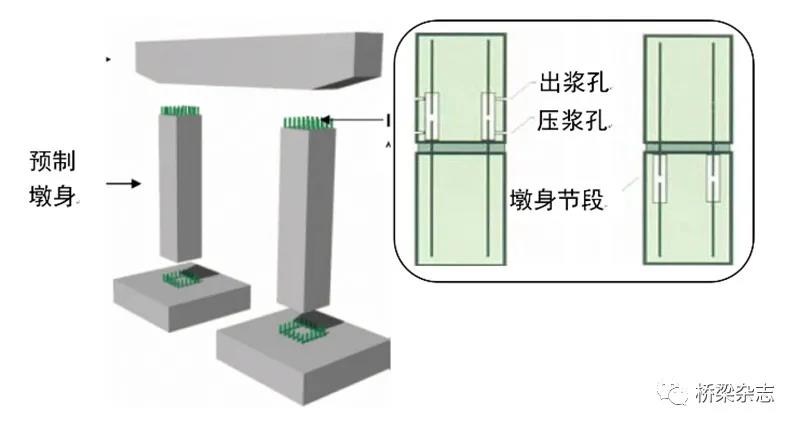
Fig. 5 connection structure of precast assembled pier and grouting sleeve
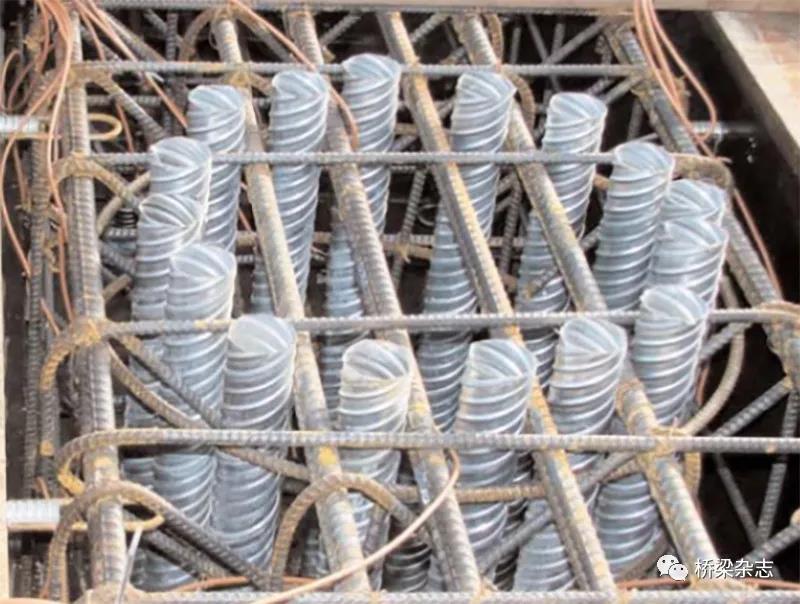
Fig. 6 grouting metal bellows connection
5. Reinforcement shall be welded or overlapped and wet joints shall be adopted
A certain amount of reinforcement shall be extended in advance for the precast assembled pier to overlap with the reserved reinforcement of adjacent components. Temporary support shall be set, and the connection parts of reinforcement shall be connected by post cast concrete (wet joint), which is also the design idea of segmental assembled pier widely used in China. The mechanical properties of piers constructed with this structure are often similar to those of traditional cast-in-situ concrete piers, but the existence of wet joints will increase the construction time and the amount of on-site reinforcement lapping and pouring. From the perspective of rapid construction, this scheme has some deficiencies.
6. Socket connection
The socket joint connection structure is to insert the precast pier body into the reserved hole corresponding to the foundation. The insertion length is generally 1.2 ~ 1.5 times the section size of the pier body. A certain thickness of mortar is laid at the bottom and filled with semi-dry concrete around. The advantage is that the construction process is simple and the on-site operation quantity is small. The disadvantage is that the mechanical behavior of the joint, especially the seismic performance, needs to be further studied. This connection structure is used for Beijing Jishuitan bridge in China and some bridges in the United States.
In addition, in recent years, some researchers at home and abroad have also proposed other types of Precast Pier body segment connection structures, such as adding energy dissipation reinforcement connection structure, hybrid connection structure, etc. However, due to various restrictions, it is still in the stage of academic research.
Fabricated bent cap
The main function of bent cap is to transfer the load borne by the main beam to the pier. At present, the common construction method is mainly cast-in-situ. The assembly type of bent cap has been preliminarily explored at home and abroad, and some attempts have been completed. According to the segmentation method, the fabricated bent cap can be divided into full precast bent cap and semi precast bent cap.
Fully prefabricated bent cap is the main method adopted for rapid construction at this stage. It is characterized by prefabrication of bent cap in transverse (or longitudinal) sections (or pieces). Only the joints are treated for on-site assembly without formwork erection and pouring. According to the segment segmentation method, it can be further divided into three categories: overall full prefabrication, horizontal segmentation, vertical segmentation and vertical and horizontal comprehensive segmentation. Semi prefabricated bent cap is a new rapid construction method, which is characterized by partial prefabrication and partial cast-in-place of bent cap. According to different prefabricated structures, it can be divided into post cast strip type and shell prefabrication.
In bridge engineering, the rapid construction method of main beam at the present stage in China can be collectively referred to as “full prefabrication of beam transverse cutting”, and this method is also used for bent cap. What is worth exploring is the treatment of connection surface of transverse cutting. According to different connection surfaces, the full prefabrication method of transverse cutting of bent cap can be further divided into: small key tooth combination assembly, large key tooth combination assembly, steel key combination assembly, corbel combination assembly, etc.
Mechanical properties of fabricated structures
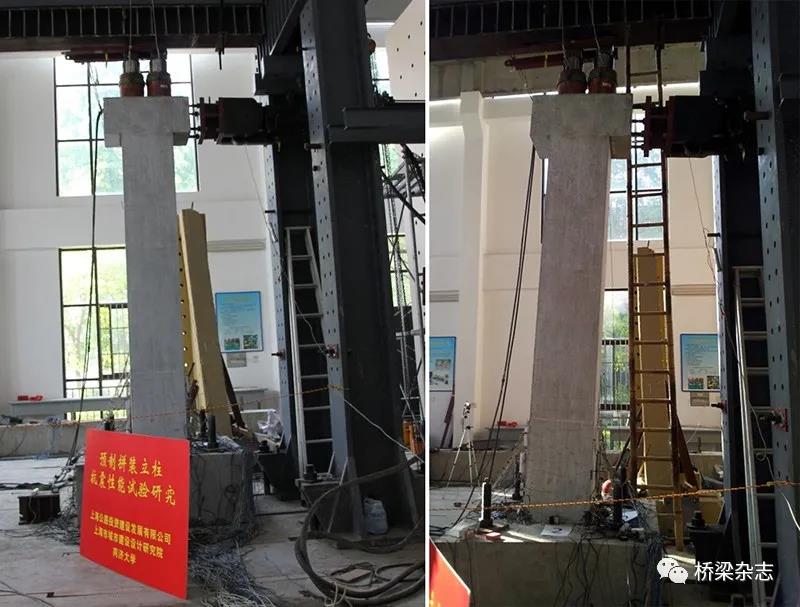
Fig. 7 actual loading diagram of test piece and diagram after loading deformation
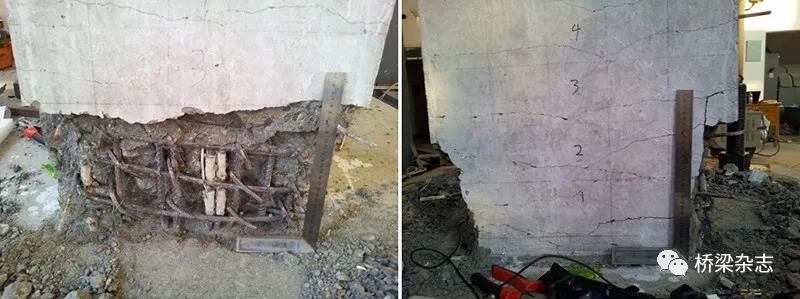
Fig. 8 failure mode of test piece
Shear and bending properties of fabricated bent cap
At present, there are many ways of prefabricated bent cap by overall prefabrication and transverse segmentation. Based on engineering practice, this paper selects a 25m large cantilever bent cap as the research object to study its shear and bending properties.
In the shear performance test, the number, position and size of key teeth between splices are considered, and a total of 5 specimens are designed. Through model test, the generation and development of shear crack, joint failure mode and shear capacity under load are studied, and the influence of test parameters on shear capacity is investigated.

Fig. 9 shear performance test of fabricated bent cap
Three specimens are designed for the flexural performance of fabricated bent cap. The test parameters include shear key type and stress type. The stress types are uniform loading and eccentric loading. According to the mechanical characteristics of large cantilever bent cap, the cyclic load loading scheme of large cantilever precast bent cap is proposed, and the loading is carried out in the normal use stage and the simulated seismic load stage.
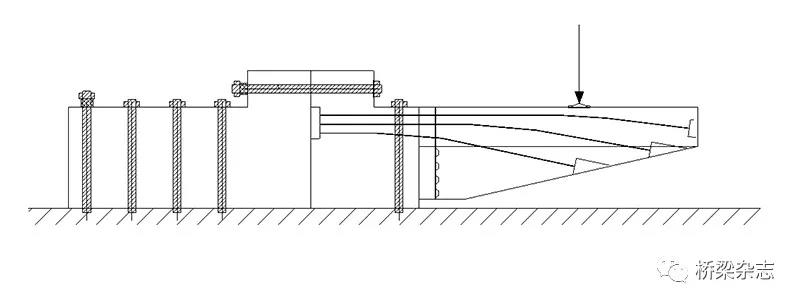
Current situation and construction of domestic standard systemAt present, the current bridge design standards in China include the industrial standards code for design of urban bridges CJJ 11-2011 and code for design of highway reinforced concrete and prestressed concrete bridges and culverts JTG 3362-2018. These two industrial standards give detailed provisions on the design of bridge structures, but there are few provisions related to fabricated bridge technology and no detailed calculation method, To a great extent, it restricts the popularization and application of fabricated bridge structure. The first domestic standard for prefabricated bridge structure, Shanghai engineering construction code technical specification for precast assembled piers (DG / TJ 08-2160-2015), prepared by Shanghai urban construction design and Research Institute (Group) Co., Ltd. in 2015, has laid a foundation for the popularization and application of prefabricated bridge technology in Shanghai and even the whole country. Industry standards such as the Ministry of communications are also being prepared.
Special key technologies in the standard
The formulation of special key technology a standard in the standard is used to guide engineering practice and facilitate the popularization and application of engineering technology. The structural design of fabricated bridges generally needs to meet the provisions of the current industrial standards code for design of urban bridges CJJ 11 and code for design of highway reinforced concrete and prestressed concrete bridges and culverts JTG 3362. However, in terms of the unique technology of fabricated bridge structure, it needs to be specified in the corresponding standards and specifications. The standard system of fabricated bridge structure needs to solve these problems, especially in the places inconsistent with the traditional cast-in-place structure. include:
1. Anchorage length of grouting sleeve connection
The application of grouting sleeve connection in building structure is relatively mature. According to the construction industry standard grouting sleeve for reinforcement connection JG / T 398-2012, the length of grouting connection end should not be less than 8 times of reinforcement diameter. The diameter of reinforcement used in the building is small, and it also bears less dynamic load. Therefore, the anchorage length can be controlled at about 8 times the diameter of reinforcement; For bridge engineering, the diameter of reinforcement used in pier column is generally large and needs to bear dynamic load. In order to ensure safety, it is reasonable to use 10 times of anchorage length.
2. Design of lifting points for prefabricated components
Another obvious difference between bridge engineering and construction engineering is the weight of prefabricated components. In building engineering, prefabricated members generally have small weight and convenient hoisting. Therefore, according to the current national standard code for design of concrete structures gb50010-2010 (2015 Edition), the lifting ring shall adopt hpb300 reinforcement or Q235B round steel. In bridge engineering, there are many precast segmental beams used before. Therefore, the current industry standard code for design of highway reinforced concrete and prestressed concrete bridges and culverts JTG 3362-2018 also stipulates that the lifting ring shall be made of hpb300 reinforcement; However, for the prefabricated bridge substructure, the weight of prefabricated components is large, and the turnover of components will be involved in the process of construction and transportation. Therefore, it is not appropriate to limit the use of hpb300 reinforcement for lifting rings. The lifting ring can be made of prestressed steel strand.
3. Inspection of grouting connectors
Difficult detection of grouting connection technology is also a problem hindering the popularization and application of fabricated bridge structures. A variety of detection technologies such as embedded steel wire drawing method, chip method and reflective ultrasonic method have been successfully developed and will be released in the newly revised local standards of Shanghai.
Industrial assembled bridge technology can not only control the project quality, but also accelerate the construction speed and reduce environmental pollution. At the same time, it also meets the development requirements of low-carbon and harmonious society. It will be a set of high-efficiency, low-carbon and environmental protection bridge construction technology, and has broad application prospects. The emergence of fabricated bridge technology is also an opportunity for industrial transformation. The government should encourage in policies, designers need to innovate in ideas, and contractors need to transform in management. At the same time, only by adhering to the overall technical development route of production, learning, research and application can we really improve the quality and performance of fabricated bridges and promote their application.
Published in this article / bridge magazine
2020 issue 3 total issue 95
Author/ Zhou Liangyan, Xing Fei, Li Xuefeng
Author unit/ Shanghai urban construction design and Research Institute (Group) Co., Ltd
edit / Sheng Chao
Us editor / Zhao Wen
Editor in charge / Chen Hui
Reviser / PEI Xiaoyin, Liao Ling